Wind turbine data independence promises a future rich with possibilities
by RES | okt 23, 2023 | Tid det tar att läsa: 4 min
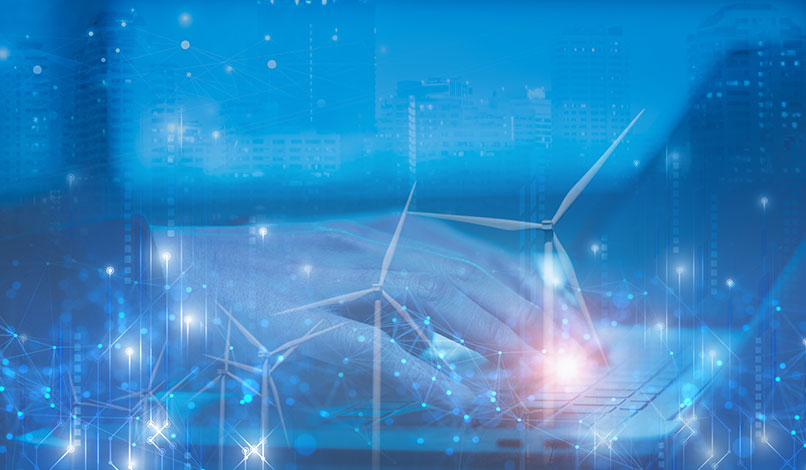
by Michael Johansen, Director of Customer Solutions, RES
Very few wind farm owners are using data generated by their wind turbines to their full advantage. Although turbines have produced a high frequency of data (raw controller data) for the best part of two decades, it has remained largely untapped by asset owners for optimising their assets’ performance because of a lack of access.
This is in part due to commercial arrangements; many OEMs provide long-term service arrangements but rarely include the provision of data for enhanced monitoring, advanced analytics, and performance optimisation purposes. After-sales 3rd party monitoring software solutions, which use low frequency SCADA data (collected every ten minutes) have risen in popularity and are useful for identifying potential issues but typically work best when complemented by other diagnostic techniques.
Like when a doctor detects a potential heart problem by listening to the patient’s chest – you get a general picture of the patient’s health in that moment but need other diagnostic tests to reveal how the heart and the body are performing on a second-by-second basis, and a broader understanding of the health potentially associated with the heart problem.
Realising the full potential of data
As technology has advanced, the unrealised value of this lack of data access has only grown larger, with its potential running into the millions of pounds across an asset’s full value chain.
If data access can be achieved, the challenge then lies in having the right people, domain expertise and business understanding to know what questions to ask of the data, and how to interpret its answers to generate meaningful outcomes and actions for actual turbine improvements. This is the challenge that RES sought to answer when it acquired Anemo Analytics in late 2022 so that it could complement and diversify the data-led services and solutions that it already offered.
By delivering more sophisticated diagnostics, more accurate decision-making processes, and enhanced predictive maintenance, it unlocks a new level of asset performance optimisation, resulting in better annual energy production (AEP) and reduced asset downtime.
The move brings more choice, competitiveness and independence to the market, allowing offshore and onshore wind asset owners to benefit from their data in a comprehensive way.
A step-by-step process for asset optimisation
Once data access is collected, it can be tempting to immediately seek to make an impact on ‘big ticket’ items such as increasing AEP, but it almost always makes sense to start with the basics: the turbine’s configuration and how all the hardware, firmware and software interact together.
Most turbines have a couple of thousand settings and it’s not uncommon to find that these have not been reviewed since the turbine was commissioned. Add in instances of failed software updates and troubleshooting issues, and you have a turbine running with faults and suboptimal settings.
Once the turbine’s configurations are refreshed to align with the current needs and expectations of the site, an assessment of fatigue loads and vibration should be completed to ensure all equipment is operating smoothly and that the rotor system is properly balanced. Even detecting and correcting a slight rotor imbalance can lessen unnecessary wear and reduce the risk of unscheduled downtime, higher OPEX costs and loss of production.
Data rich with possibilities
With the site’s site parameters optimised and a baseline established, the team can perform more complex analysis to reveal potential variations in performance and opportunities for improvement. Comparing the expected power curve with the actual output in its current configuration is always a good place to start which, in order to avoid relying on misleading wind speed measurements, is done through an evaluation of the driving turbine control scheme for the specific OEM and turbine platform. Then moving on to assess blade aerodynamics and yield under-performance mitigation. If blade furniture is installed, it is good practice to revisit the turbine’s controller settings to ensure the settings are optimised for the new hardware and the revised aerodynamic profile of the blades.
Turbine data can also be used for more novel ways for example to optimise health and safety and compliance. On a remote site in Texas, specific turbines were initially commissioned to stop production when ice was detected to protect staff onsite. However, as time had passed the critical turbines nearby the technician office were now operating with standard settings whereas other non-critical turbines were having stop alarms during icing. This meant a range of turbines were being stopped needlessly while others that needed to be stopped weren’t.. One parameter change instantly increased annual energy production while also improved health and safety.
There are also numerous opportunities to enhance workforce efficiency while also improving safety. Periodic blade calibration work requires technicians to enter a confined space. With data analytics, technicians can be much more accurate in their calibration work, shortening the overall process and time spent in confined spaces. Ongoing proactive monitoring for mass imbalance also ensures that costly onsite inspections are only completed when necessary. When applied more widely across the site, it will significantly reduce the time spent by technicians on unnecessary inspections, allowing them to focus on the most at-risk, complex and high value pieces of equipment instead and leveraging their experience and skills where it matters most.
These are just a couple of examples of how gaining independent access to data and having the right subject matter expertise to dive deep into the variations within it can create a step change in the efficiency of the wind industry. Data independence has the potential to create substantial improvement across asset performance touching on everything from annual energy production and uptime to workforce efficiency and operating costs. But, to date, we have just scratched the surface of what is possible; gaining data independence opens a world rich with possibilities, a new frontier to explore full of exciting unknowns.