Solutions
Our passionate and experienced people deliver successful clean energy projects globally.
Technologies
Driving a clean energy future through state-of-the-art renewable technologies.
See all technologiesResources
Browse our latest resources, including company updates, customer stories, industry insights, and research reports.
See all resourcesCareers
Join a collaborative team of passionate individuals who engage in meaningful, stimulating, and world-changing work.
Learn moreAbout RES
We live our mission, celebrate the people making it happen and transform the way the world produces and consumes energy.
See about usOur offices
Like our business, we’re truly global – but proudly local. Find contact and location details for every RES office.
Contact us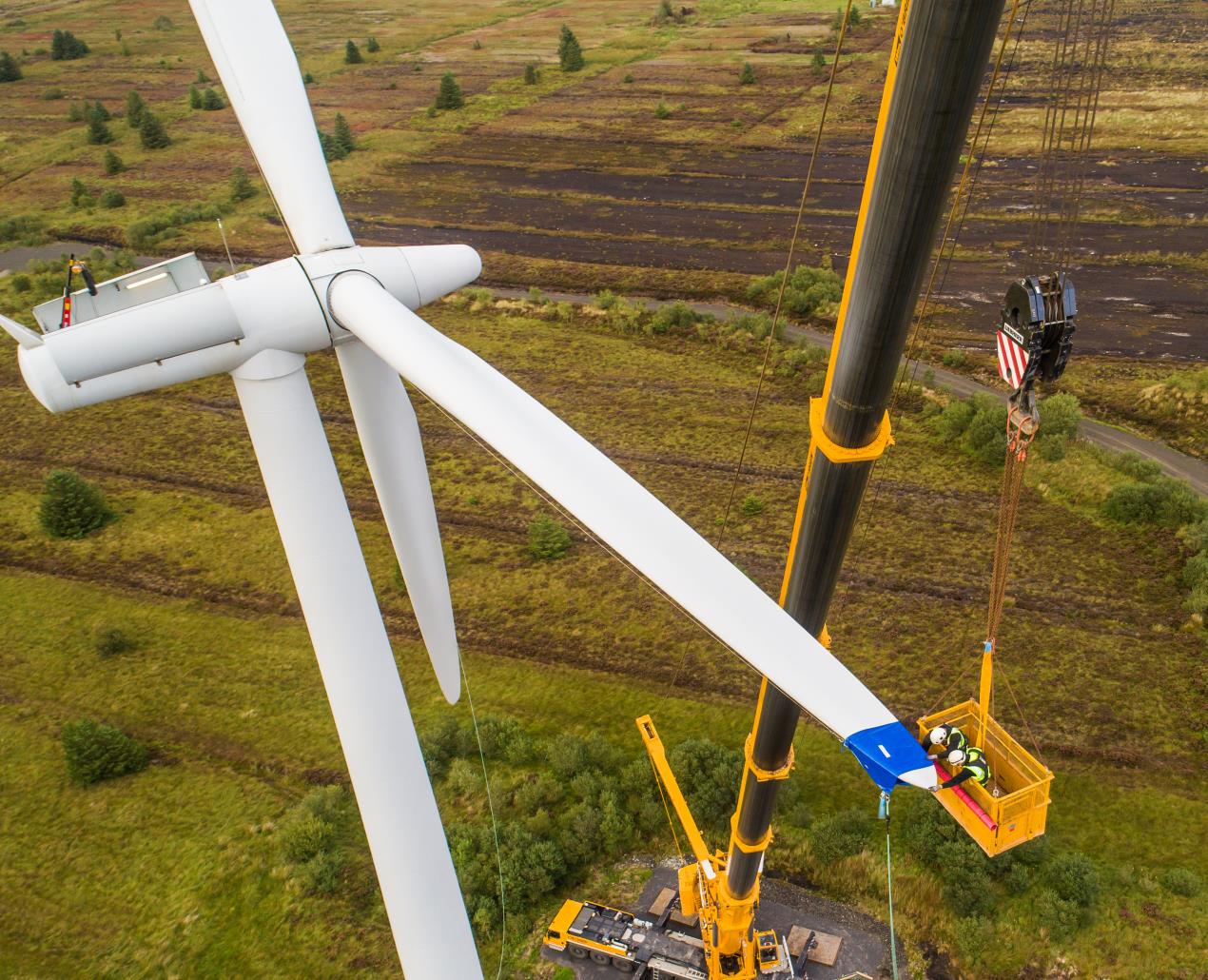
For a long time, perception has been that the most expensive and biggest item to replace on a wind turbine is the gearbox, which is why most maintenance strategies prioritise this. Diego Kieffer, Turbine Maintenance Manager, discusses why there is a need to place more emphasis on preventative blade maintenance.
All blades will suffer some form of deterioration over their lifetime, which will affect the Annual Energy Production (AEP) of the wind turbine. Often, effort and resource is spent monitoring and carrying out proactive maintenance works to the turbine, whereas blade maintenance hasn’t traditionally been prioritised. However, with new technology, increasing rotor diameters and greater tip speeds it is essential that more emphasis is given to this area.
In our experience as both an asset manager and O&M provider, we’ve seen that the most common types of blade repairs are leading-edge erosion and damages near the tip. Leaving this until the damage becomes more severe runs the risk of expensive repairs and significant downtime. In a worst-case scenario, a catastrophic blade failure could cost upwards of £1M.
Of course, we understand that there is no infinite budget for maintenance. This is why we have been working on ways to reduce the costs of blade maintenance for clients. For instance, forecasting using AEP losses enables us to prioritise repairs meaning that we can maximise the number we can carry out across the portfolio within the short weather window. This ensures that assets are performing to their full potential as the more urgent issues are rectified sooner than later. For one client, by prioritising and distributing repairs over a three-year period, we saved £650K on repair costs and AEP losses, as well as minimised the risk of any blades requiring replacement.
With the significant increase in rotor diameters, we believe that standardisation in the industry is required to help us increase our knowledge on newer blade performance and maintenance requirements. Standardisation allows owner/operators to understand the damage as well as wear and tear trends on each wind farm to help better plan blade maintenance accordingly. If owners could rely on the information being provided, we can dedicate more time into analysing the data to optimise our maintenance strategy.
The lack of standardisation creates grey areas on maintenance contracts, the owner and O&M contractor will have a different interpretation on what damages are covered under the maintenance contract, leading to extended conversations on responsibilities before any works can be done. This can delay the repair of blades past the blade season (Spring/Summer) which then results a costlier repair. The situation has improved in recent years but there is still a lot of work to do in this area. We are working to raise awareness of this issue.
Advances in technology are enabling us to make better decisions and improve maintenance strategies. Using AI and machine learning, we can predict failures better as opposed to waiting for them to happen. Digitalisation will speed up decision making process and help determine the most cost-effective strategy. By using this to enhance blade maintenance strategies and prioritising this area, we will not only save in the long run, but help to add more green energy to the grid by preventing downtime.
For more information contact [email protected]