Solutions
Our passionate and experienced people deliver successful clean energy projects globally.
Technologies
Driving a clean energy future through state-of-the-art renewable technologies.
See all technologiesResources
Browse our latest resources, including company updates, customer stories, industry insights, and research reports.
See all resourcesCareers
Join a collaborative team of passionate individuals who engage in meaningful, stimulating, and world-changing work.
Learn moreAbout RES
We live our mission, celebrate the people making it happen and transform the way the world produces and consumes energy.
See about usOur offices
Like our business, we’re truly global – but proudly local. Find contact and location details for every RES office.
Contact us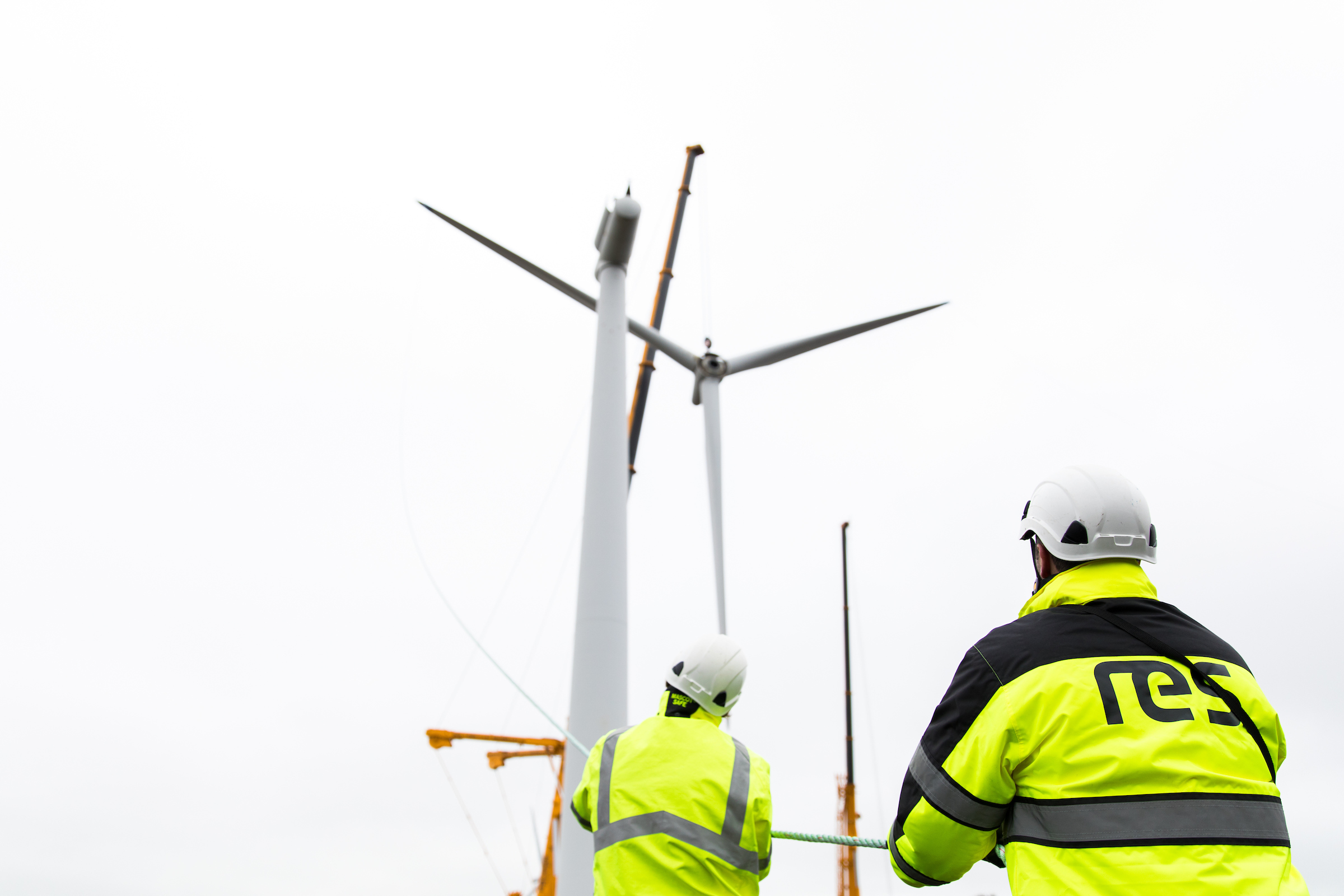
By Brian McDaid, Head of Turbine O&M, RES
Main component failure is common in the wind industry – so much so that RES has an entire team dedicated to replacing them. It’s not that main components such as gearboxes, bearings and generators are particularly prone to breaking down, it’s that there are so many in operation now that failures are an expected part of wind farm operations and maintenance (O&M).
With lead times for some components averaging between three and six months, it is critical that parts are ordered ahead of time. Unexpected failure can lead to significant downtime, resulting in expensive repair costs and extensive drops in revenue and yield, consequently reducing renewable energy supplied to the grid with overall substantial losses.
Integrating inspection techniques new and old
The introduction of condition-based monitoring has helped to revolutionise the industry, allowing wind farm maintenance teams to line up replacement components before a failure occurs, without having a costly stockpile tucked away in a warehouse.
At Taurbeg Wind Farm in Ireland, for example, our in-house condition monitoring system detected an issue with a main shaft on one of the 2.3MW wind turbines. The lead time for the component was a lengthy nine months. Thankfully, as the issue was spotted early, the replacement could be carefully planned, and catastrophic failure avoided. As a result, the turbine was offline for less than a week, rather than several months, which saved the client £120k in what could have been lost revenue.
A decidedly more human factor for avoiding main component failure is the power of attention to detail. Many experienced engineers will know if an oil reading isn’t quite right or if something sounds off; identifying and addressing minor issues early often saves significant time and money in the long term. This is a skill that we must consciously pass down to the next generation of wind turbine engineers and one of many reasons why we are so proactive in training apprentices, upskilling our workforce, and fostering a genuinely inclusive and family-friendly place to work.
Although sensors are slowly digitalising this incredible skill, they do not yet give a comprehensive picture. At RES we pair sensor insights and engineering experience with more unusual techniques such as ultrasound and measurement inspection. This inspection technique is particularly good at detecting potential failures and maintenance needs on slow-moving bearings and for components with low levels of vibration. On a recent site inspection of 75 blades, we were able to identify 19 defects that may have otherwise been missed using ultrasound.
The weather window has the final say
Once a potential main component failure has been identified, the replacement clock begins ticking. The weather then becomes the maintenance team’s biggest challenge. If you are replacing a blade for example, you want the weather to be almost completely flat – it’s designed to catch the wind, but that’s not what you want when it’s on the crane! With wind farms typically sited in locations with higher mean wind speeds, it can be difficult to find a three-to-four-day weather window during which a mobile crane can safely assist with replacement, and when downtime will have the least impact on revenue.
The team closely monitors the weather conditions and keeps in constant contact with the crane operator to ensure it is mobilised only when weather conditions will allow safe operation, with decisions to go ahead often only made 24-72 hours in advance. Having a crane arrive on site but unable to operate is a costly misstep which has led to some interesting innovations to watch out for, such as cranes that are built directly into the turbine tower that can safely operate at higher wind speeds. In addition, meteorological software is advancing all the time, supporting asset operators to better predict changeable weather conditions, and overcome the uncontrollable nature of the weather.
Main component replacement is a fine art, combining inspection and monitoring innovation with deep industry knowhow. A well-executed replacement can be the difference between having a turbine offline for several months, costing tens of thousands of pounds, or planned for just a few days in a month when production will be at its lowest. While it’s unlikely we’ll ever see an invention that controls the wind, with such high stakes, it pays to have a highly skilled team onboard that can sense main component failure before it happens giving ample weather windows to choose from for replacement work.