Solutions
Our passionate and experienced people deliver successful clean energy projects globally.
Technologies
Driving a clean energy future through state-of-the-art renewable technologies.
See all technologiesResources
Browse our latest resources, including company updates, customer stories, industry insights, and research reports.
See all resourcesCareers
Join a collaborative team of passionate individuals who engage in meaningful, stimulating, and world-changing work.
Learn moreAbout RES
We live our mission, celebrate the people making it happen and transform the way the world produces and consumes energy.
See about usOur offices
Like our business, we’re truly global – but proudly local. Find contact and location details for every RES office.
Contact us-
Home
/
Resources
/
Case Studies
/
Ultrasound & Measurement Inspection
Ultrasound & Measurement Inspection
by RES | Jun 28, 2023 | Reading time: 2 min
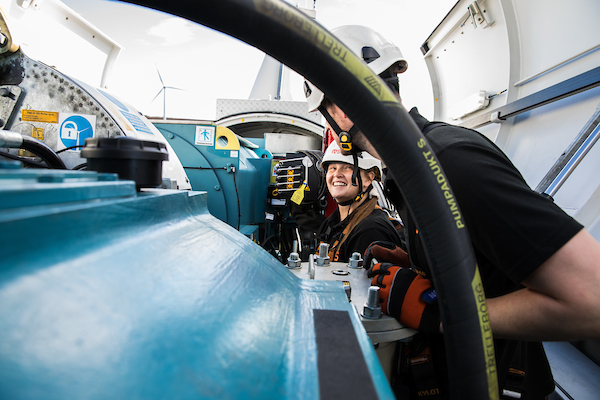
RES was asked by a wind site owner to complete a blade bearing ultrasound and measurement inspection for a wind farm located near Edinburgh in Scotland.
The existing operator was aware that there were defects on the site, but the full extent wasn’t clear meaning that planning future works was difficult. Whilst RES does not operate or maintain this site, we are one of only a handful of O&M providers that provide a Blade Bearing Ultrasound and Measurement Analysis Service. Despite ultrasonic testing of mechanical and electrical systems being widely used in other sectors, its use within onshore wind is still relatively new.
RES has utilised this method for several wind farm owners and operators to help verify issues being highlighted by their existing O&M contractors, as well as to help plan future works on O&M contracts.
We have also used the technique to verify issues for clients and have been proven successful in identifying lubrications starvation and bearing defects.
The work
RES completed a blade bearing ultrasound and measurement inspection across the site which consists of 25 Nordex N80 2.5MW turbines – 75 blades in total.
This type of inspection provides a predictable diagnostic capacity due to its high frequency and short wavelength which easily filters out background noise and focuses in on a relevant component. When changes begin to occur in the ultrasonic range, there is still time to plan appropriate maintenance.
Ultrasonic testing is particularly useful for fault diagnosis on slow moving bearings and low-level vibration which can’t be picked up by other nondestructive testing (NDT) methods. This makes it extremely useful to use on blade and main shaft bearings as well as hydraulic and electrical faults.
Results
RES helped the existing operator understand the full extent of existing defects in order to plan future works.
Following our survey, we found 19 defects and categorised the level of wear indicated to show which bearings require attention more so than others. We provided a full report to the existing operator who could then complete further assessments and plan future works to avoid more serious failures occurring and revenue losses for the owner.
Follow up inspections are planned in the future to help manage the progression of possible failures and assess the effectiveness of the remedial works carried out following the initial inspection.